Pressureless sintering is a process that diffuses and densifies materials between silicon carbide powder particles at high temperatures (usually above 1600°C) without external pressure. Pressureless sintered silicon carbide ceramics are made of high-purity, ultrafine silicon carbide powder as raw materials, with a small amount of sintering aids (such as boron, carbon, etc.) added, and sintered at high temperatures in an inert gas or vacuum atmosphere at atmospheric pressure. The resulting product is almost completely dense and has excellent mechanical properties.
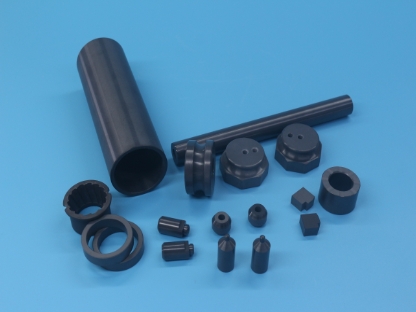
silicon carbide ceramic parts produced by Mingrui Ceramics.
1. Overview of pressureless sintering process
Pressureless sintering is a process that diffuses and densifies materials between silicon carbide powder particles at high temperatures (usually above 1600°C) without external pressure. Its advantages include:
Low cost: no complex pressurizing equipment is required, the process is simplified, and it is suitable for large-scale production.
Complex shape molding: ceramic parts with complex geometric structures can be prepared to meet diverse needs.
Uniform microstructure: High-temperature sintering promotes uniform growth of grains, forms a dense structure, and improves the overall performance of the material.
2. Performance advantages of pressureless sintered silicon carbide ceramics
Ultra-high hardness and wear resistance
The Vickers hardness of pressureless sintered silicon carbide ceramics is close to that of diamond (Mohs hardness 9-9.5), which is significantly better than traditional ceramics such as alumina and silicon nitride. It has excellent wear resistance and is suitable for high-wear environments.
High-temperature stability and oxidation resistance
It can still maintain stable mechanical properties in high-temperature environments above 1600°C, and has a low thermal expansion coefficient (about 4.0×10⁻⁶/°C), strong thermal shock resistance, and is suitable for applications such as high-temperature furnaces and aerospace thermal protection systems.
Excellent corrosion resistance
It has strong corrosion resistance to chemical media such as acids, alkalis, and salts, and is suitable for corrosive environments such as chemical equipment and oil pipelines.
High thermal conductivity and electrical properties
The thermal conductivity is much higher than that of ordinary metals, which can dissipate heat quickly. It also has low dielectric loss and high insulation, and is suitable for heat dissipation substrates of electronic devices and high-frequency electronic components.
Biocompatibility and lightweight
Non-toxic and harmless, suitable for medical implants (such as artificial joints, dental prostheses); low density (about 3.1 g/cm³), with both lightweight and high strength in bulletproof equipment.
3. Application fields of pressureless sintered silicon carbide ceramics
Industrial manufacturing
Cutting tools and wear-resistant parts: tools for processing high-hardness materials, mining machinery linings, etc.
Energy and chemical industry
Chemical reactors and pipelines: corrosion resistance ensures the stability of equipment in strong acid and alkali environments.
Heat exchangers and nuclear energy components: high thermal conductivity and neutron absorption capacity are suitable for nuclear reactor control materials.
Electronics and Electrical
Power semiconductor heat dissipation substrate: silicon carbide substrate is used in 800V high-voltage systems of new energy vehicles to improve heat dissipation efficiency.
High-frequency electronic devices: Low dielectric loss characteristics support 5G communication filters and radar systems.
Aerospace and Military
Rocket nozzles and turbine blades: High temperature resistance optimizes engine thrust and combustion efficiency.
Electromagnetic protection and armor: Lightweight and high-strength characteristics improve the anti-penetration ability of composite armor, and silicon carbide power devices enhance the stability of electronic warfare equipment.
Medical and Bioengineering
Implantable medical devices: Biocompatibility supports the application of orthopedic implants and dental restoration materials.