Silicon Carbide Ceramic Substrate Semiconductor Silicon Carbide (SiC) Wafers and Substrates
- Materials:Alumina (Al2O3)/ Zirconia(ZrO2) /Si3N4 /SiC
- Sizes:Mini-OD: 0.02mm;Max-length: 500mm
- Delivery times:2 -25 days(depends on the quantity)
- Precision:Ra 0.1um tolerance: 0.001mm... etc
- Features:High hardness, high strength, low density, high temperature resistance, wear resistance and corrosion resistance
- Customized:Can be custom for special sizes and shapes
1. Factory price and shipment within 24 hours In stocks
2. MOQ:1qty
3. Payment Term: PayPal; T/T; L/C etc.
4. Shipment: by sea by air by courier by post etc.
Wear-resistant silicon carbide ceramic substrates Semiconductor silicon carbide ceramic wafers
Ceramic substrates and ceramic wafers made of silicon carbide and other materials produced by Mingrui Ceramics
As an important electronic material, silicon carbide ceramic substrates have excellent thermal conductivity and can effectively conduct heat from electronic components to maintain a stable operating temperature of electronic components. The insulation performance of silicon carbide ceramic substrates is also a major advantage, and they are suitable for electronic devices that require high insulation.
Silicon carbide ceramic substrates not only have high bending strength, but also have excellent high-temperature mechanical properties (such as strength, creep resistance, etc.) among ceramic materials. In particular, materials sintered by hot pressing, pressureless sintering, and hot isostatic pressing can maintain high-temperature strength up to 1600°C.
Silicon carbide ceramic substrates also have excellent corrosion resistance and high-temperature resistance, and can operate stably for a long time in harsh working environments.
The manufacturing process of silicon carbide ceramic substrates mainly includes raw material preparation, molding, drying, sintering, and post-processing. Among them, sintering is one of the key steps, which needs to be carried out in a high-temperature environment to ensure that the ceramic board achieves the required structure and performance.
Application fields of silicon carbide ceramic substrates
1. Electronic packaging: Silicon carbide ceramic substrates play an important role in the field of electronic packaging, especially in the packaging of high-power electronic devices. They can be used as heat dissipation bases to improve the heat dissipation performance and long-term stable working ability of devices.
2. Optoelectronics: Due to its excellent optical properties and high thermal conductivity, silicon carbide ceramic substrates are widely used in the preparation of high-power lasers and high-brightness LED devices.
3. Semiconductor processing: The high thermal conductivity and chemical stability of silicon carbide ceramic substrates make it an ideal choice for semiconductor material substrates, which helps to improve the growth rate and uniformity of semiconductor materials.
4. Chemical industry: In the chemical industry, silicon carbide ceramic substrates can be used to prepare linings and seals for chemical equipment, improving the service life and safety of equipment.
5. Aerospace: Due to its excellent high temperature resistance and mechanical strength, silicon carbide ceramic substrates can be used to prepare thermal isolation materials and structural parts for aircraft engines, which helps to reduce the weight of aircraft and improve fuel efficiency.
Delivery:
Custom OEM will be shipped within 15 days after determining the parameters
The samples will be shipped within 3 days
Quick Delivery Via Fedex,DHL,UPS,TNT Etc.
Support customer to designate shipping company
For more informations (the price,delivery time,moq etc)about the ceramic plates, please contact us or email:admin@cerampart.com
Machining process
Powder forming->forming by lathe->Sintering in furnace-> crack testing with red ink->surface grinding with big water grinding machine to make the both ends smooth->
cylindrical grinding to make out diamater and groove/ steps okay->grinding the length size okay with big water grinding machine-> drilling of holes and chamfer with CNC machine.
-> ultrasonic cleaning-> quality checking.
Mingrui ceramic parts property
· Flexural strength |
· Chemical resistance |
· Electrical insulation |
· Corrosion resistance |
· Low thermal conductivity |
· Wear resistance |
· Temperature resistance |
· Heat resistance |
· High voltage |
· Hardness... |
Ceramic materials(include but not limited belows)
· 95%--99.99% Alumina (Al2O3) · Silicon Carbide · Silicon Nitride · TTZ: Magnesia partially stabilized Zirconia (ZrO2)
· YTZP: Yttria partially stabilized Zirconia (ZrO2) · ZDY: Yttria fully stabilized Zirconia (ZrO2)...
|
Al 2O 3 |
ZrO2/Y2O3 |
ZrO2/MgO |
MgO |
SiC |
Si3N4 Reaction sintered |
Si3N4 Hot pressed |
ALN |
Physical properties |
|
|
|
|
|
|
|
|
Density (g/cm3) |
3,9 |
5,9 |
5,75 |
3,58 |
3,2 |
3,27 |
3,29 |
3,26 |
Molecular weight (g/mole) |
102 |
- |
- |
40,4 |
40,1 |
140 |
140 |
41 |
Maximum service temperature air (°C) |
1700- 1800 |
1500 |
1000 |
2200 |
1500 |
1200- 1500 |
1100- 1600 |
1000- 1800 |
Mechanical properties |
|
|
|
|
|
|
|
|
Hardness (Mohs) |
9 |
- |
- |
5,5 |
9 |
- |
- |
7 |
Modulus of elasticity (GPa) |
300-400 |
200 |
200 |
250-300 |
420 |
170-220 |
280-310 |
318 |
Poisson's ratio |
0,25 |
- |
- |
0,18 |
0,14 |
0,25-0,26 |
0,27 |
0,25 |
Fracture toughness (MPa.m1/2) |
2-3 |
7-13 |
6-10 |
- |
2,5-3,5 |
3,5-5 |
6,1 |
4,5 |
Electrical properties |
|
|
|
|
|
|
|
|
Dielectric constant |
9-10 |
- |
- |
9-10 |
- |
10 |
10 |
9,2 |
Electrical resistivity at 20°C (Ohm.cm) |
>10 14 |
10 13-10 14 |
>10 10 |
- |
10 2-10 6 |
>10 7 |
10 12- 10 15 |
>10 14 |
Dielectric strength (kV/mm) |
10-20 |
9 |
2-10 |
- |
- |
- |
- |
15 |
Thermal properties |
|
|
|
|
|
|
|
|
Specific heat (J/K/kg) |
900 |
400-500 |
420 |
870-880 |
750 |
690 |
680-800 |
800 |
Thermal conductivity (W/m/K) at 20°C |
26-35 |
2,2-3,2 |
1,5-2,5 |
40-50 |
63-155 |
9-30 |
15-43 |
180 |
Coefficient of thermal expansion ( 10-6) from 20 to 1000°C |
8-9 |
10-11 |
5-16 |
10-13 |
4-5 |
3 |
3,3 |
4,4-5,3 |
Melting point (°C) |
2050 |
2590 |
- |
2800 |
2500 |
1900 |
1900 |
2200 |
Customization & Machining Service:
As a ceramic parts manufacturer,us offer a wide of the ceramic specification,and customized&machinables. Get a Quote On Your Customized Now!! or up a files by EMAIL.
Our Custom Capabilities:
1.High Purity Martoxid Powder
2.OEM Support, More Than 10 Technicians With 5-Year R&D Experience
3.35000 ㎡workshop, annual output could reach hundred million pieces.
4.All crafts are inspected strictly based on drawings,checked each month.
5.Best Service And Quick Delivery Via Fedex,DHL,UPS,TNT Etc.
|
|
Technical reference of manufacture |
Dimensional accuracy |
Up to 0.001mm |
Concentricity |
Up to 0.003mm |
Parallelism |
Up to 0.002mm |
The inner hole tolerance |
The minimum 0.005mm |
Straight flute |
The narrowest 0.1x100mm |
The thickness of the size |
Minimum to 0.02mm |
The screw thread |
Minimum internal thread M2 |
Cylindricity |
Up to 0.004mm |
The linear tolerance |
Up to 0.001mm |
The smallest aperture |
The minimum 0.07mm |
Precision process |
CNC maching,grinding,lapping |
Surface finish |
Glazed,polishing or metallized
|
|
FAQ
1. Monthly Capacity: 50,000-60,000 pcs;
2. Material: OEM or as per your suggestion;
3. Lead time: about 7-20 days, pls confirm the quantities required;
4. Incoterm: FOB, CFR, CIF;
5. Delivery Cost: It is determinated by the destination port;
6. Payment Term: PayPal; T/T; L/C.
7. Shipment: by sea, by air, by courier, by post, etc.
Feedback
1. For any query or doubt, please contact us firstly, we will update with you soon;
2. For any other satisfaction, please also feedback to us, which could improve our service better and better.
For more information about ceramics parts,please contact our engineers in time >>> |
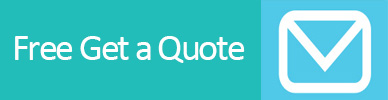
|