High purity alumina ceramic insulator is a technical ceramic component for power equipment made of high purity alumina material. The following is a detailed introduction to high purity alumina ceramic insulators:
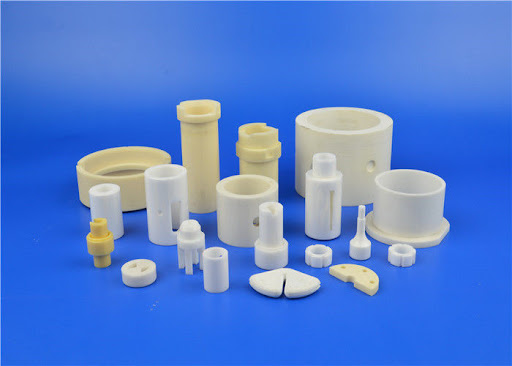
High temperature resistant alumina ceramic insulation parts.
1. Material composition
The main raw material of high purity alumina ceramic insulator is high purity alumina. This material has many excellent physical and chemical properties, such as high thermal conductivity, high insulation capacity, corrosion resistance, high melting point and extremely high hardness, making it an ideal choice for manufacturing insulators.
2. Performance characteristics
Excellent insulation performance: High purity alumina ceramic insulator has extremely high resistivity, can withstand extremely high current, and ensure the insulation safety of power equipment.
High temperature resistance: The melting point of alumina is very high, so that ceramic insulators can remain stable in high temperature environments and are not easy to deform or melt.
Corrosion resistance: Alumina ceramics have good corrosion resistance to a variety of chemical substances and can be used for a long time in harsh chemical environments without damage.
High strength: Alumina ceramics have high hardness and mechanical strength, can withstand large external forces and pressures, and ensure the stability and reliability of insulators during use.
3. Application fields
High-purity alumina ceramic insulators are widely used in various power equipment due to their excellent performance, such as:
Transmission lines: used to support and fix conductors to prevent current leakage and short-circuit accidents.
Substations: In substations, ceramic insulators are used to isolate and support high-voltage equipment to ensure the safe operation of power systems.
Signal cables: In signal transmission systems, ceramic insulators are used to protect signal cables from external interference and damage.
4. Production process
The production process of high-purity alumina ceramic insulators mainly includes raw material preparation, molding, sintering, glazing and packaging processes. Each link needs to be strictly controlled to ensure the quality and performance of the product.
Raw material preparation: Select high-purity alumina powder material, and after screening, drying, grinding and other treatments, ensure that the particle size of the raw material is uniform and remove impurities.
Molding: According to different insulator structures and sizes, different molding methods, such as injection molding, pressing, etc., are used to form the required shape and structure.
Sintering: The molded insulator is placed in a special sintering furnace for high-temperature heating, so that the powder material undergoes a chemical reaction at high temperature to form a dense crystalline structure.
Glazing: Apply a layer of insulating coating on the surface of the insulator to improve the insulation performance and stain resistance of the insulator.
Packaging: The produced ceramic insulators are packaged to prevent damage during transportation and use.