Aluminum nitride (AlN) ceramic sheets have shown significant advantages over alumina (Al₂O₃) and zirconia (ZrO₂) ceramic sheets in multiple key performance indicators and application scenarios. The following is a specific comparative analysis:
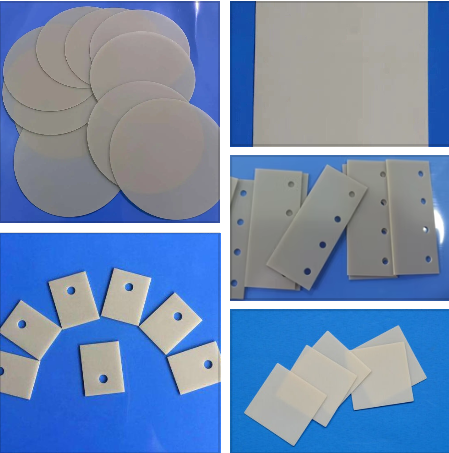
Aluminum nitride ceramic sheets produced by Mingrui Ceramics
1. Thermal conductivity
· Aluminum nitride: The thermal conductivity is as high as 170-200 W/(m·K), and the theoretical value can reach 320 W/(m·K), which is close to the level of metallic copper, 5-10 times that of Alumina, and 7 times that of zirconia.
· Alumina: The thermal conductivity is only 24 W/(m·K), and the heat dissipation performance is weak.
· zirconia: The thermal conductivity is even lower (about 2-3 W/(m·K)), which is almost unsuitable for high heat dissipation demand scenarios.
· Advantages: Aluminum nitride can quickly conduct heat in high-power electronic devices (such as IGBT, LED, and 5G RF devices) to avoid overheating and failure of the device.
2. Thermal expansion coefficient matching
· Aluminum nitride: The thermal expansion coefficient is 4.5×10⁻⁶/K, which is close to semiconductor materials such as silicon (Si) and gallium arsenide (GaAs), significantly reducing the risk of interface peeling caused by thermal stress.
· Alumina: The thermal expansion coefficient is 7.2×10⁻⁶/K, which is quite different from semiconductor materials and can easily cause thermal mismatch problems.
· zirconia: The thermal expansion coefficient is about 10×10⁻⁶/K, and the matching is worse.
· Advantages: Aluminum nitride has higher reliability in scenarios where direct contact with chips is required, such as semiconductor packaging and power modules.
3. Electrical insulation and dielectric properties
· Aluminum nitride: Resistivity >10¹⁴ Ω·cm, low dielectric constant (about 8-9), and low high-frequency signal transmission loss.
· Alumina: The resistivity is comparable to that of aluminum nitride, but the dielectric constant is higher (about 9-10), and high-frequency applications are limited.
· zirconia: The dielectric constant is higher (about 30-35), and the electrical insulation is weaker, which is not suitable for high-frequency circuits.
· Advantages: Aluminum nitride is suitable for high-frequency, high-power RF devices (such as 5G base stations) and integrated circuit packaging.
4. Mechanical and chemical stability
· Aluminum nitride: 300-400 MPa bending strength, high temperature resistance (decomposition temperature 2450℃), resistant to molten metals (such as aluminum, gallium arsenide) corrosion, and plasma corrosion.
· Alumina: Flexural strength is similar to that of aluminum nitride (300-400 MPa), but poor high temperature and corrosion resistance (melting point 2050℃).
· zirconia: Higher flexural strength (800-1000 MPa), excellent toughness, but poor thermal conductivity and high temperature resistance (melting point is about 2700℃, but thermal stability is lower than aluminum nitride).
· Advantages: Aluminum nitride performs better in high temperature and corrosive environments (such as semiconductor manufacturing equipment and nuclear reactors), while zirconia is more suitable for wear-resistant parts.
5. Environmental protection and safety
· Aluminum nitride: non-toxic and harmless, replacing toxic beryllium oxide (BeO) to become the mainstream choice.
· Alumina/zirconia: Although non-toxic, alumina has insufficient performance in some scenarios (such as high-power radio frequency), and zirconia is expensive and difficult to process.
· Advantages: Aluminum nitride is in line with environmental protection trends and is widely used in safety-sensitive fields such as medical equipment and the food industry.
6. Comparison of application fields
Aplication |
AlN |
Al₂O₃ |
ZrO₂ |
High power electronic heat dissipation
|
Core substrates (IGBT, LED)
|
Low power devices
|
Not applicable
|
RF devices
|
5G Amplifiers, filters
|
Low frequency, low power circuits
|
Rarely used
|
High temperature/corrosive environments
|
Semiconductor equipment, nuclear power components
|
Traditional industrial refractory materials
|
Wear-resistant parts (such as bearings, knives)
|
Biomedical
|
MRI equipment, implants
|
General medical equipment
|
Dental restorations, artificial joints
|
Aluminum nitride ceramic sheets are significantly superior to alumina and zirconia in terms of high thermal conductivity, thermal matching, high-frequency performance, and high-temperature/chemical stability, and are particularly suitable for high-power electronics, 5G communications, aerospace and other high-end fields. Alumina still dominates the low-end and mid-end markets due to its low cost, while zirconia has an advantage in the wear-resistant field due to its high toughness. In the future, with the optimization of aluminum nitride preparation technology (such as thick film slurry development and low-temperature sintering process), its cost is expected to decrease and its application range will be further expanded.