Porosity size distribution of zirconia ceramics on sintering and microstructure
Time: 2021-01-28 Writer: mingrui
Porosity size distribution of zirconia ceramics on sintering and microstructure
Some zirconia ceramics have a lot of pores on the surface, while others are particularly smooth and have almost no pores. So what is the reason? In fact, it has a great connection with the sintering of zirconia ceramics.
Zirconium oxide ceramics can be used as both functional materials and carriers, additives or active components of industrial catalysts, and plays an important role in the reaction of CO2 with H2 to synthesize methanol. There have been many reports on the effect of pore size distribution on the development of sintering and microstructure. The change in the pore size distribution of the same powder body is often caused by the agglomeration of primary particles. Studies have shown that not only the density but also the densification rate is greatly affected by the pore size distribution.
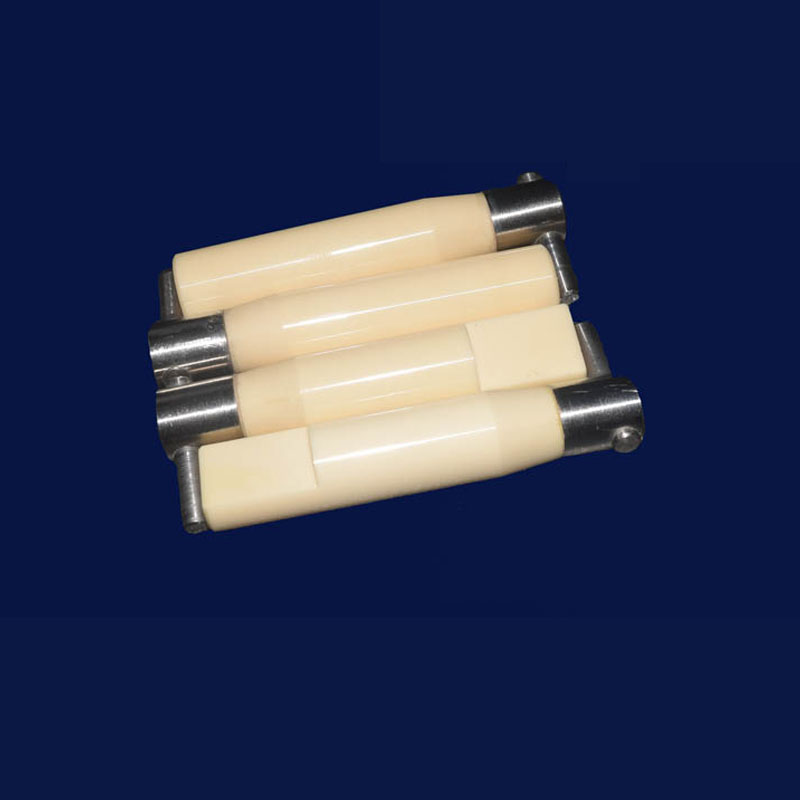
Studies on microscopic scabs have found that the more atmospheric pores in the green body, the lower the sintered density. In extreme cases, when the pore size is bimodal, the pores between the agglomerates, or so-called secondary pores, can hardly be ruled out. It has been found that although grain growth is affected by the phase structure, the powder and green body properties (silver density, pore size distribution) do not affect grain growth in the green body during heating and holding.
Although the properties of ceramic green bodies such as density do not affect grain growth, they affect the size ratio of pores to particles. The properties of the green body do not affect the grain growth, but affect the pore growth, so it also affects the densification behavior. The relationship between grain size and density in the initial stage of densification is as described above. There is a linear relationship between grain size and density in the middle stage of sintering. According to the definition of the sintering stage, only the densification is carried out at the initial stage of sintering without grain growth.
This phenomenon may exist in a green body having a large initial particle size, but for a green body composed of an ultrafine powder such as ultrafine zirconia used in the present study, grain growth and compactness are performed even in the initial stage of sintering. It is also produced almost simultaneously. This result means that for the solid phase sintering of the ultrafine powder, the initial stage of sintering can be approximated as non-existent or at least negligible.
From this, we can draw the following conclusions:
1 The grain growth in the green body is not affected by the properties of the molded body。
2 The pore growth is controlled by grain growth and densification. The former causes the pores to grow synchronously with the grains while the latter causes the pores to shrink, the pore R value decreases, and the pore growth is affected by the properties of the molded body;
3 The initial stage of sintering of ultrafine powder is almost negligible, grain growth and densification occur simultaneously. From the beginning of the burning to the end of the medium term, the grain size is linear with the density. This linear relationship can be based on grain growth and densification. Generated by the same diffusion mass transfer mechanism, and the dependence of grain growth and density on temporal phase in the isothermal process is explained;
4 The linear relationship between grain size and density is affected by the properties of the molded body, because the grain growth is driven by the chemical position of the difference in particle size, and the densification is promoted by the sintering compressive stress acting on the pores;
5 Higher dihedral angle, molding density, narrow particle and pore size distribution are beneficial to move the grain size density relationship track to high density and small grain size.