Zirconia Ceramics Production Process 9 Kinds of Technology Can Save Energy
Time: 2018-12-08 Writer: mingrui
In the production process of zirconia ceramics, energy is mainly consumed in spray drying pulverizing, semi-finished drying and roller kiln firing, so improving the energy efficiency of these three links is the main way to save energy in industrial ceramic production enterprises, among which the energy saving of roller kiln firing link is the most important. The following from the process to talk about industrial ceramics energy-saving technology.
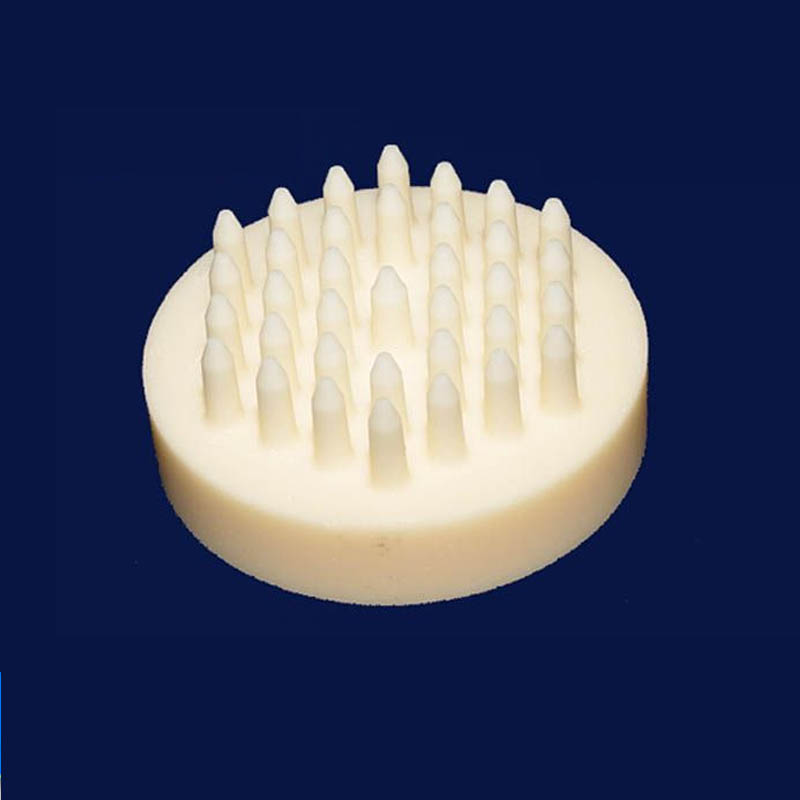
(1) Selection of raw materials Raw materials are an important foundation for the production of industrial ceramics, for large-scale industrial production, the requirements of raw material performance to meet production needs, stable quality, appropriate price.
Therefore, new technical requirements are put forward for raw material source and mining and processing.
① Research and development of new raw materials and low-temperature rapid burning technology, expand the source of raw materials, reduce transport costs, to achieve energy conservation.
② uses specialized production, commercialization supply, at the same time the development of washing, sorting, pre-homogenization treatment, efficient crushing, variable speed ball mill, high efficiency iron removal and other technical equipment.
③ the implementation of raw materials standardization, the physical and chemical properties of raw materials long-term stability in a relatively small range, stable supply, improve the yield.
(2) Ball Mill
① Ball Mill adopts long life, small load of ball mill, large effective volume and many lining of loading.
② selects high efficiency water reducer to improve ball grinding efficiency.
The decrease of mud moisture makes the proportion of raw materials and the effective space in ball mill increase, improve the efficiency of ball grinding, and the output of spray drying tower is greatly improved.
③ to develop a reasonable ratio of material, ball, water and spherical stone.
④ using frequency conversion technology, starting current can be 3-5 times smaller than the original, to achieve real soft start, eliminate the impact of the start, extend the service life of the machine shaft, gears, belts and other mechanical parts, reduce maintenance costs, at the same time can easily set the grinding time, grinding time and automatic shutdown function, so that the operation is more intelligent, humanized.
⑤ the use of continuous ball mill, ball grinding when the discharge of complete automation, no need for downtime, easy to make thick pulp, so that the back of the spray drying process to save energy, can save energy consumption 10%-35%.
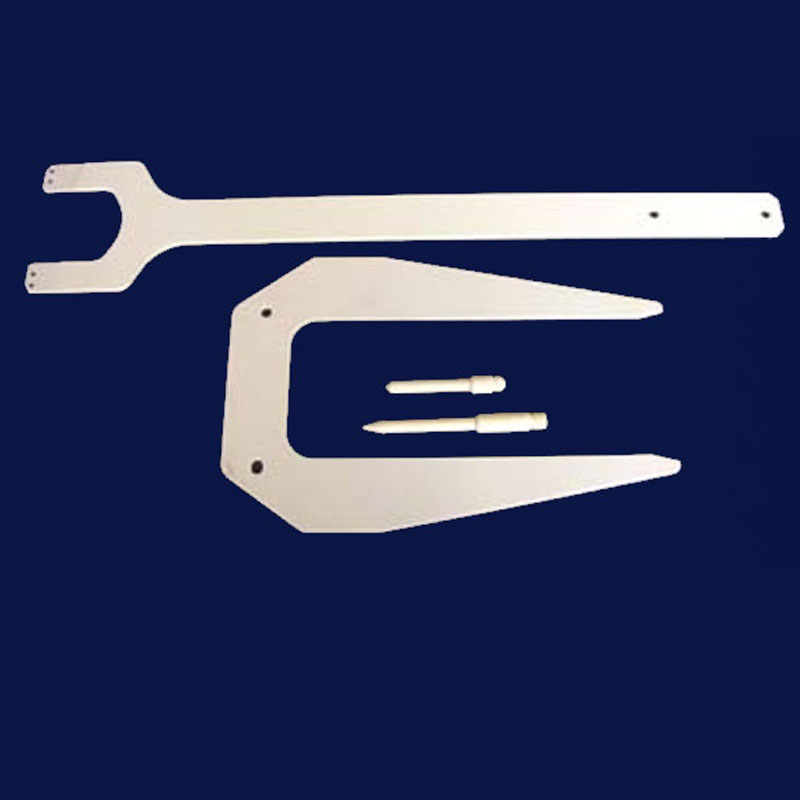
(3) Spray Drying powder
① reduces mud moisture and optimizes the type and proportion of water reducer while optimizing process formulations.
② Rational use of recycled fine powder, the cyclone dust collector collected from the fine powder and spray drying tower to make powder with a belt to the silo, to achieve the purpose of uniform mixing, rather than the fine powder discarded or re-pulping.
③ uses dry granulation, instead of the traditional ball mill and spray drying pulverizing two processes, can save fuel 70%-80%, water saving 70%-75%, power saving 30%-50%. However, because the dry powder contains high iron, dry powder fluidity is poor, the prepared product performance is not as good as the traditional process, therefore, it is necessary to improve the process.
(4) Pressing molding
① uses large tonnage, energy-saving press.
Large tonnage press pressure is high, the brick quality of the suppression is good, the pass rate is high, under the condition of equal yield, the power consumption is less, and the energy saving effect is obvious.
② uses frequency conversion network technology in the fabric system, which makes it easy for operation managers to better understand the operation status of production site and automatic control equipment, to optimize the production process parameters, shorten the time of fault detection, reduce labor intensity, and improve the efficiency of production labor. It can not only save electricity, but also reduce the generation of waste.
(5) Semi-finished drying
① uses multi-layer drying technology to improve thermal utilization, reduce floor space and increase production scale.
② uses forced convection rapid drying technology, the hot air through the hair dryer on the upper and lower surface of the brick vertical injection, to achieve brick forced convection drying, while ensuring the uniform heat of the brick, uniform drying, uniform temperature.
③ uses the waste heat recycling technology, causes the hot air to cycle repeatedly in the equipment, maintains the constant temperature, the humidity, the quantification small discharge, makes full use of the energy, reduces the discharge, realizes the brick fast drying.
(6) Sintering process
① adopts a sintering process, compared with two sintering, the energy consumption of one sintering is much smaller, but because of the high requirement of the composition and glaze of the billet, the process has certain technical difficulty.
② uses a low temperature fast burning process, not only can increase production, save energy consumption, but also can reduce costs.
③ using pre-sintering technology, when the molding, the billet does not go through the drying process, and direct fast drying and pre-sintering, its maximum temperature in 900 ℃ or so, this stage of porcelain billet is not sintered completely, but there is enough hardness and strength to complete the glaze and other processes, the final billet, Glaze sintering together to complete, only need to 10-15min. This process can be used for relatively low raw materials, resulting in an overall savings of 40% of the energy consumption in the manufacturing process.
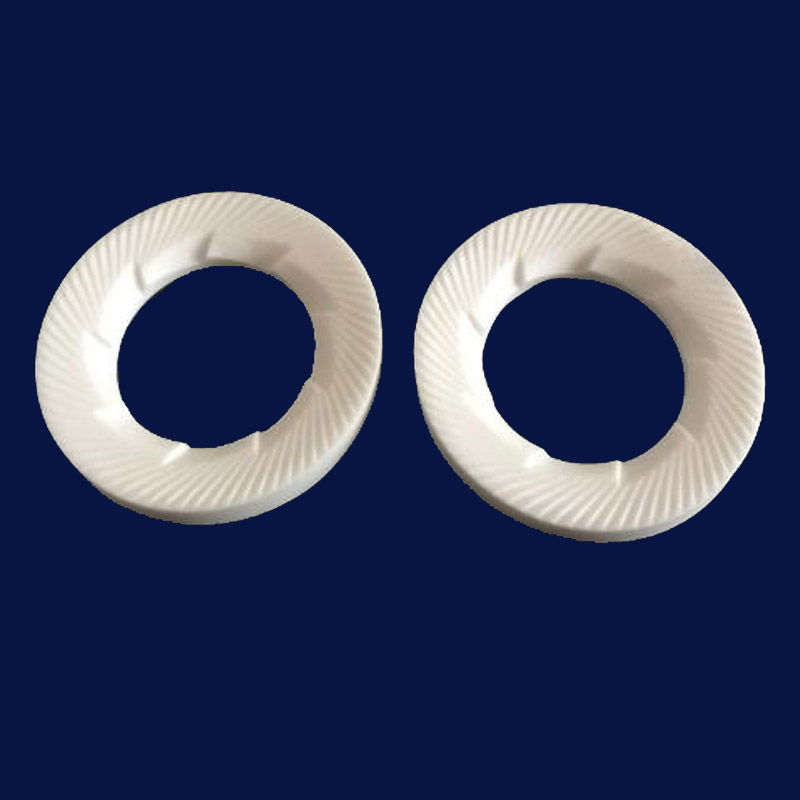
(7) Glaze
① selects advanced equipment to reduce glaze loss.
In the whole process of glazing, there are generally 15%-20% losses, most of which are difficult to recycle, and measures should be taken to recycle them.
② uses inkjet printing technology, the technology can realistically express the texture and color of the selected material, showing the design effect of ceramic tile stereoscopic surface, and in a short period of time to achieve consumer personalized aesthetic needs, greatly shorten the production cycle.
(8) Wet grinding edge The use of semi-dry grinding free drying technology, through the grinding edge water nozzle and grinding head insulation, so that brick in the grinding process to greatly reduce the amount of water inhalation, direct packaging into the warehouse, without the need for subsequent drying treatment.
(9) Other energy-saving technologies
① strengthen product structure adjustment, improve independent innovation ability, increase product added value.
② reduces distribution losses by optimizing design, shortening distribution lines, selecting suitable cross-sectional conductors, and configuring reasonable distribution equipment.
Install power capacitors to increase the factor.
③ actively promote the implementation of green lighting projects, and actively promote the use of high-pressure sodium lamps, fluorescent lamps and other new energy-saving lamps.
Optimize the lighting design of the plant, make full use of natural light to achieve lighting energy saving.
④ to strengthen enterprise energy-saving management, the development of energy-saving reward and punishment system.
⑤ established an energy management center.