Process design principle of CNC machining ceramic products
CNC process design principles for ceramic products
Centralized ceramic processing process, precise positioning of the ceramic reference
Fine and accurate positioning can be precisely processed ceramic workpiece surface position, and in order to reduce positioning errors, it is necessary to CNC machine tool processing ceramics procedures together, with a unified benchmark to locate.
Based on this, CNC machining ceramic process designer should take the surface as a fine reference, arranged in the beginning and end of CNC machining ceramic process, in order to lay a fine basis for subsequent processing procedures, speed up the processing of ceramics.
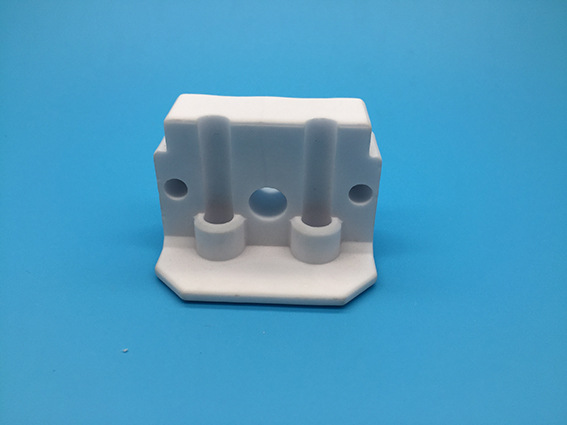
CNC machining ceramic process designer should also set the auxiliary benchmark, in order to unify the design, programming and calculation of the benchmark.
First rough machining, then semi-finishing, and then finishing
In order to accelerate the speed of CNC machining ceramics, make full use of the uniformity of finishing allowance.
In the process of machining ceramics, rough machining should be carried out first to reduce the cutting times and save a lot of machining allowance by using the depth of large cutting.
Then, after the rough machining is completed, semi-finishing is arranged to be carried out. Because some residual uniformity left after the rough machining cannot be fully utilized in the finishing, therefore, semi-finishing can be used for further processing to make full use of the machining allowance of the rough machining, so as to improve the machining quality of the workpiece surface.
And the final shape of the workpiece is actually formed by the last uninterrupted machining, so CNC machining process designer should consider the position of the tool in and out of the tool, it is best to be able to pay attention to the tool replacement when the workpiece does not form a continuous contour, to avoid the workpiece surface scratches because of the change in the cutting force.
Generally speaking, no matter which side of the workpiece, it should follow the order of rough machining, then semi-finishing, and then finishing, so that the product produced has a better finish and higher fineness.
The principle of being near and within
In the process design of CNC machining ceramics, it is very important to master the distance between the machining position and the cutter point.
CNC machining ceramic process designer to follow the principle of proximity, the first processing from the knife point distance to the nearest part, and then processing and the knife point distance from the far part, as far as possible to reduce the moving distance of the tool.
For example, if the rigidity of the cutting tool is not good, the cutting heat will affect the sharpness of the tool and cause the shape and size of the inner surface of the workpiece to be out of control. However, the principle of proximity can keep the semi-finished product relatively rigid during the cutting process of the CNC car [2].
Therefore, CNC machining process design should follow the principle of proximity, the first processing from the knife point distance parts, then processing from the knife point far parts;
In order to improve the working efficiency of NC machining, first process the inner surface of the workpiece and then process the outer surface of the workpiece.
Select the shortest route to reduce the number of program segments
The path of cutting refers to the path of the cutting point from the beginning to the end of the machining, the path of the moving of the cutting point plus all the paths of returning to the cutting point, including the path of cutting.
In the ceramic cutting process, the cutting path is generally based on the workpiece contour, the confirmation of the cutting path determines the rough cutting path.
Therefore, under the condition that the quality of ceramic parts is stable, choose the most appropriate tool path, can save the number of processing time, reduce tool consumption, reduce mechanical wear.
In addition, for the preparation of ceramic processing program, CNC machining ceramic process designer should also pay attention to make the program easy to use, reduce the number of segments of the program, so as to reduce the amount of computer memory and error times, improve the quality of CNC machining ceramics.