What are the manufacturing procedures of stainless steel and zirconia ceramic composites?
Time: 2020-07-08 Writer: mingrui
What are the manufacturing procedures of stainless steel and zirconia ceramic composites?
Zirconia ceramics are mainly divided into precision zirconia ceramics and ordinary zirconia ceramics, many people do not know zirconia ceramics, zirconia ceramics have many advantages, the use of zirconia ceramics processing more and more products.In industrial production, many enterprises need to use zirconia ceramic processing parts, compared with other materials, zirconia ceramic parts performance is better, so how long is the service life of zirconia ceramics?
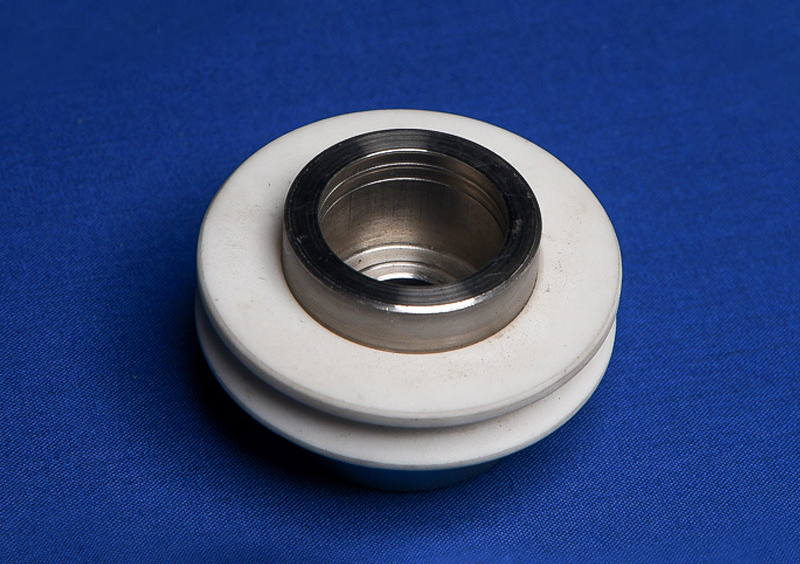
Zirconia ceramics usually last one year.Because of the death of nitrifying bacteria, some of the bodies will be washed away with the current, but some will remain in the voids of nitrifying bacteria, which will gradually accumulate in the back and block the voids.Ceramic ring parasitic effect will be gradually reduced, so the need for regular replacement.
Over time, you will find that the color of "ceramics" is "white" - "yellow" - "deep yellow", this is because the impurities in the water have blocked up the surface gap of "ceramics", even cleaning will not achieve satisfactory results!
Ordinary alumina ceramic system is divided into 99 porcelain, 95 porcelain, 90 porcelain, 85 porcelain and other varieties according to the content of Al2O3, sometimes Al2O3 content in 80% or 75% also classified as ordinary alumina ceramic series.Among them, 99 alumina ceramic materials are used for making high temperature crucibles, fireproof tubes and special wear-resistant materials, such as ceramic bearings, ceramic seals and water valves.Alumina ceramics are mainly used as corrosion-resistant and wear-resisting parts.Because part of talc is often mixed in 85 porcelain, the electrical property and mechanical strength are improved. It can be sealed with molybdenum, niobium, tantalum and other metals, and some of them are used as electrical vacuum devices.
When it comes to ceramic materials, everyone tends to associate them with fragility. However, alumina ceramics are actually superior to traditional ceramics in terms of physical properties due to the addition of special materials.The hardness of qualified alumina ceramics is very high, and no damage will occur in the case of extrusion and collision.
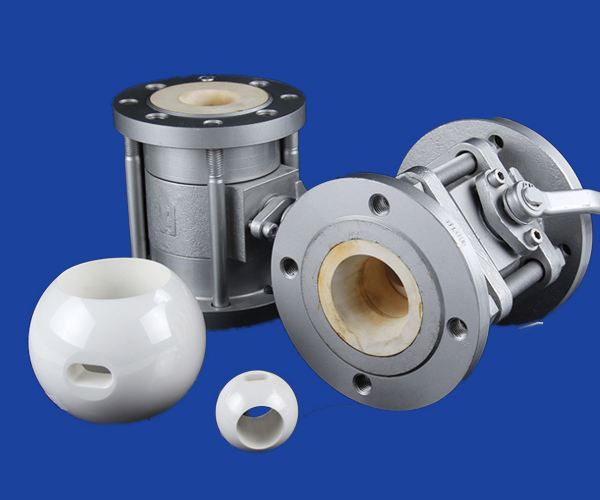
Zirconia ceramics themselves have very excellent performance, if it is combined with high-quality stainless steel materials, the advantages of this composite is not more obvious?But to make sure that the stainless steel can be combined with zirconia ceramics, and then in the gradual operation.Zirconia ceramics by virtue of high toughness, high bending strength, high wear resistance, as well as excellent thermal insulation performance, thermal expansion coefficient and other advantages favored by users.Now it has a number of major unique, that is to combine with stainless steel sintering, to make a stainless steel and zirconia ceramic composite.
In the actual production, the required materials should be prepared first. In addition to stainless steel pieces and zirconia ceramic pieces, molybdenum foil and nickel foil are also needed as auxiliary materials.The nickel layer is then deposited on the surface of the zirconia ceramic parts. The process is simple, as long as the zirconia ceramics, molybdenum foil, nickel foil and stainless steel parts are put together in a connecting mold.
In this way, the molybdenum foil and nickel foil are sandwiched between the zirconia ceramic piece and the stainless steel piece, with the molybdenum foil adjacent to the nickel metal layer on the zirconia ceramic piece and the nickel foil adjacent to the stainless steel piece.Then the connecting mould is put into a hot pressing sintering furnace to make the zirconia ceramic parts, molybdenum foil, nickel foil and stainless steel parts solid phase diffusion connection under a protective atmosphere, and then the stainless steel and zirconia ceramic composite parts are obtained.
After the workpiece is cooled, it can be removed from the hot - pressed sintering furnace, resulting in the aforementioned stainless steel and zirconia ceramic composite.Since the melting point of zirconia is higher than that of stainless steel, stainless steel will generally melt before zirconia, as long as the above method, the two can be well combined.
To pay attention to the details of the process, operation problems, as well as the vacuum furnace, a good product must have a full set of process specifications, in order to determine the product quality of standardization, zero failure, flow, modular and other characteristics.Only in this way can customers buy and use the rest assured.